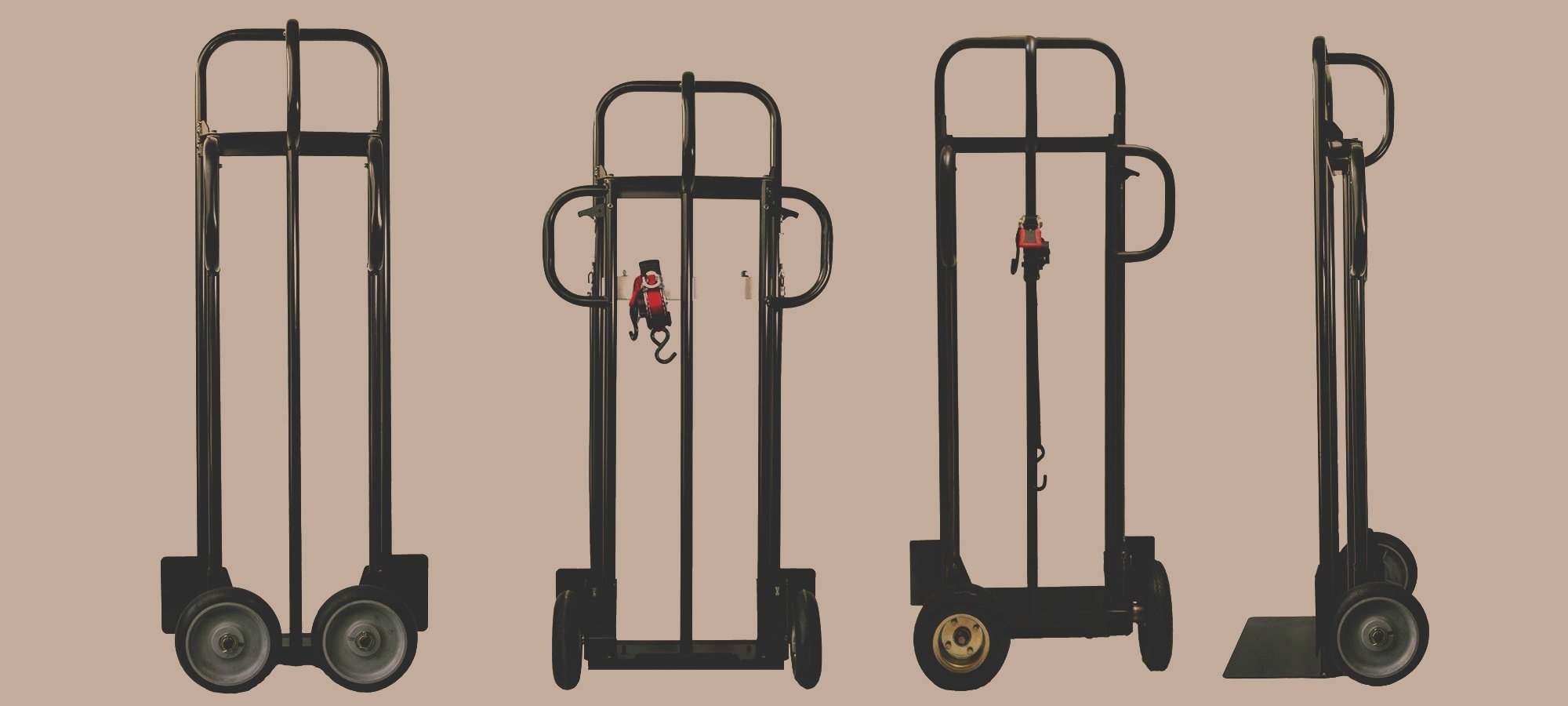
SAFETY BENEFITS
The Hand Truck Company Solutions: Reducing Workplace Injuries & Enhancing Safety
Workplace injuries related to overexertion remain the leading cause of injury, accounting for 22.7% of all incidents and costing industries $13.3 billion annually—a figure that continues to rise. Additionally, falls, object-related injuries, and bodily reactions contribute another 35.7% of workplace injuries, totaling $20.9 billion in costs.
Our 360 Hand Truck line is specifically designed to mitigate these risks by addressing awkward load shifts and reducing physical strain. Each hand truck features an integrated retractable ratchet strap, allowing for secure horizontal or vertical load stabilization without requiring manual placement or excess effort. The multi-directional wheel system, controlled by ergonomic fingertip triggers, enables effortless steering adjustments at 45, 90, and 180 degrees. This eliminates the need for heavy lifting when changing direction, reducing unnecessary force and minimizing the risk of musculoskeletal injuries.
By incorporating these innovative safety features, The Hand Truck Company enhances workplace efficiency, reduces injury-related costs, and prioritizes employee well-being.
We’re Serious About Safety
Watch a three-part video series featuring a postural analysis tool explaining how our 360 Hand Trucks reduce the risk of injury.
Reviews
“It is an easy answer to avoiding thousands of dollars in workers' comp payouts. The Hand Truck 360's fingertip-accessible triggers help transition the wheels (at 45, 90, 180 degrees) either individually or together to provide multiple control options.”
Josh Corbin, OTR/L, Licensed Occupational Therapist
OUR MISSION
Front-line workers are often injured moving items in tight spaces. The labor shortage is affecting everyone. At The Hand Truck Company, we believe that safety should always come first. Why not meld safety and increase productivity with our multi-directional Hand Truck 360 Pro with attached Erickson retractable ratchet? One team member can now safely do the moving work of two.